Technology, Innovation & Bespoke Solutions
Utilising technology to develop custom, innovative solutions and products that eliminate operational delays, increase throughput and improve safety.
Development of custom, bespoke solutions and products is a key part of BEC Engineering’s portfolio.
BEC has led the way in understanding, defining and implementing bespoke, technology-driven solutions and products for complex problems.
We can provide specialist expertise and experience in the fields of:
- Application and solutions development in Low-level development tools such as C#/.NET, C++ for Linux and Windows IOT
- Database and big data analystics and programming.
- IOT and low power applications.
- Network and communications systems design.
- Operating systems and network protocols.
- Robotics and automated vehicle design and implementation.
- Data, satellite, mobile, fibre, RF and microwave communications solutions.
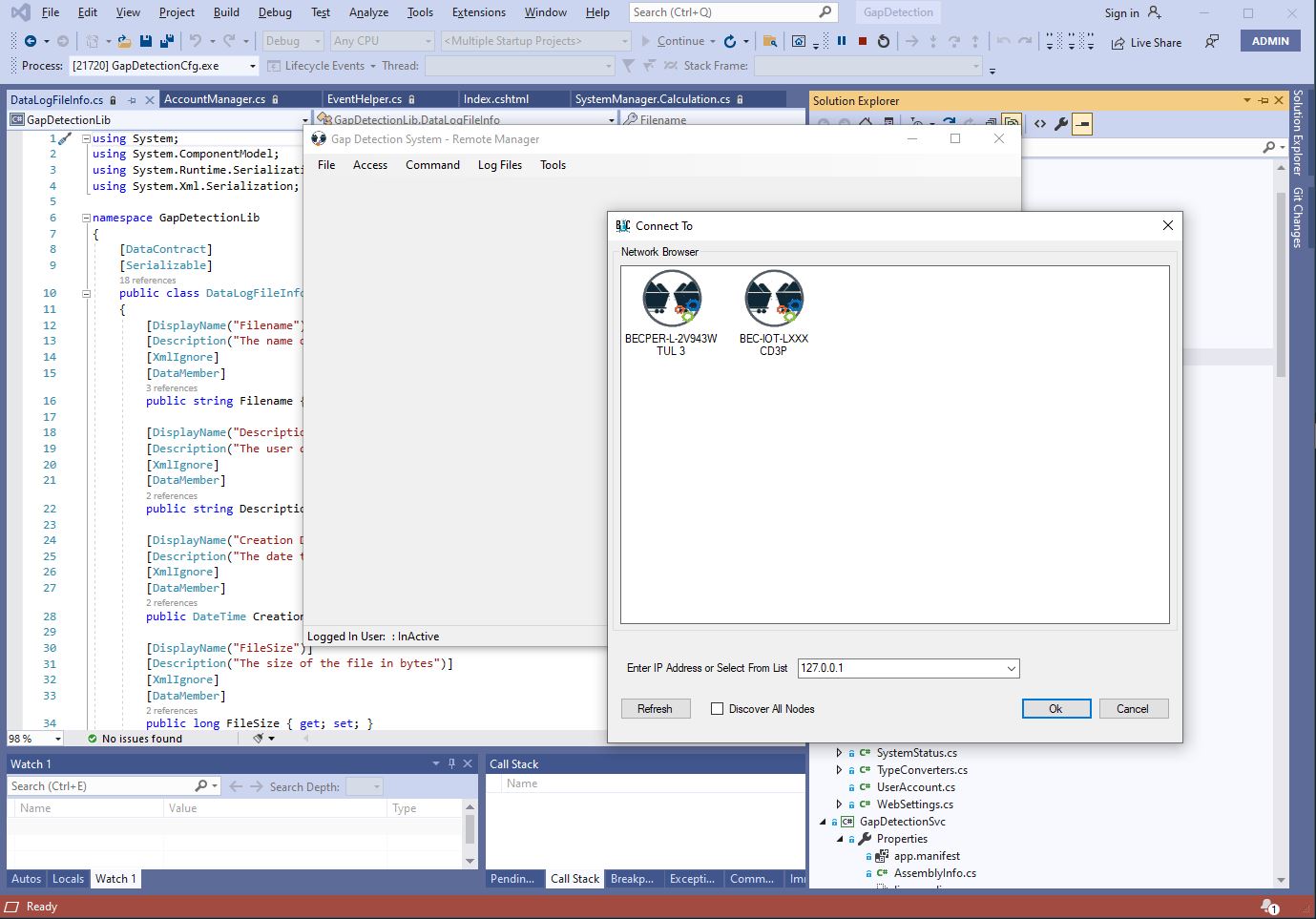
Our OEM solutions include:
- Laser Partially Dumped Ore Car Detection System – Ore car volumetric profiling system
- Laser Gap Detection System – Ore car indexer gap detection system.
- Conveyor Bulk Measurement System – Volumetric profiling and edge detection of bulk material on conveyors
- Collision Avoidance System – Active sensors detect and report any objects that come into closed contact with vuneranble parts of ship loaders, stackers and reclaimers (boom and portal)
- Reclaimer Face-up Optimisation System – Radar based solution for determining position of the stockpile edges, benchs and total height.
- Vessel Berth Monitoring – Monitors and reports the relative position shift of a vessel from its berthing location
- Advanced Volumetric Loading System – Volumetric profiling of ore and grain wagons to ensure precise, accurate loading
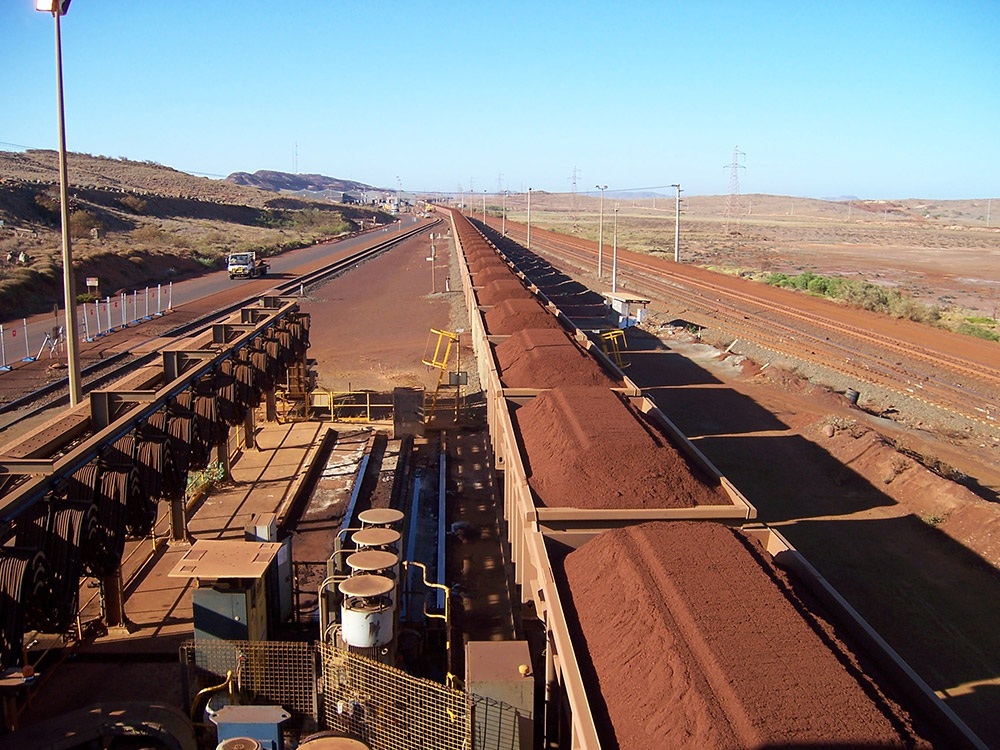
Laser Ore Car Profiling System
The Laser Ore Car Profiling System (LPDOC) is the system of choice for measuring and reporting the volume of residual ore in rail wagons following the car dumper cycle.
Ore wagons that are not fully unloaded (Partially Dumped) pose an operational risk to safe, efficient rail operations due to the imbalance of ore remaining in the wagon.
Developed and supported by BEC Engineering, the system has been selected and deployed across multiple port ore handling facilities for the worlds premier iron ore miners (BHP, Rio Tinto & FMG) and has proven to be an essential reliable, and safety-focused aspect of bulk handling operations.
The PDOC system is a standalone sensor that accurately measures the residual volume of ore remaining in a wagon following the dumping cycle.
Utilising 2-Dimensional laser scanning technology, the system:
- Profiles each wagon as it exits the car dumper and measures the volume of residual ore.
- Reports alarms and status to the PLC to stop the forward motion of the indexer in the event of a partially dumper ore car.
- Support the operator in making corrective actions by providing measurement data and 3D visualisation of the profiling wagon.
The PDOC 3D Visualisation server automatically displays the 3D scan of each ore car as it is processed on the remote operator’s console, enabling fast and efficient evaluation and corrective action following a PDOC event.
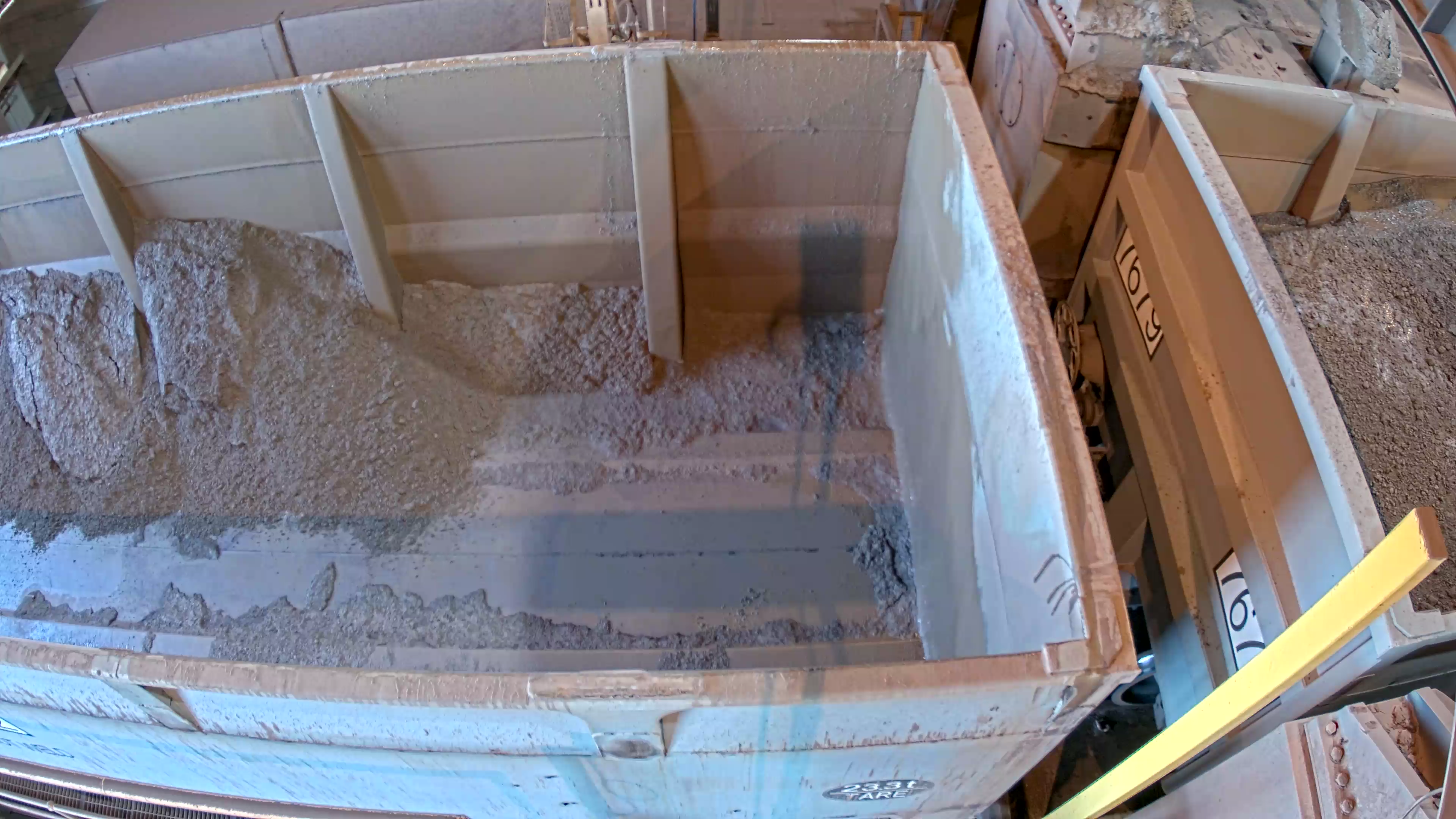
Laser Gap Detection System
The Laser Gap Detection System (LGAP) provides a reliable solution to the problem of automatically locating the gap between the two ore cars to position the train indexer for correct arm insertion.
Building on BEC’s experience in laser scanning technology, The LGAP system will monitor, detect and measure to millimetre accuracy the position of the ore car gap left, right and centre position and provide these points to the indexer control system; thereby enabling highly accurate positioning of the Indexer for arm insertion and First Car Find.
LGAP also enables the real-time positioning of the arm to account for rake dynamics and eliminates the need for PE cells and light boards that are a constant source of downtime. The system is completely standalone and can be easily configured and monitored using a standard web browser or remote configuration tool.
Status information is continuously provided to the control system via industrial protocols, including Modbus TCP, Ethernet IP and SRTP.
See the powerpoint below for an overview of the system…..

Conveyor Bulk Measurement System
The Conveyor Bulk Measurement System (CBMS) is a complete turnkey solution to the problem of detecting, reporting and logging of ore volume, available capacity and belt drift on conveyor systems.
The system provides key metrics on bulk conveyors that when incorporated into the site control system, can provide real productivity and throughput gains to material handling operations.
The system incorporates laser scanning technology to reliably:
- Profile the bulk material to determine flow rates
- Measure the bulk edges relative to the belt edges so as to maximise loading capacity
- Monitor belt location and alert on belt drift
- Detect potential ore spillage and assist in avoiding it
- Communicate key measures, alarms and status to the Control System PLC
- Record all measured data for failure mode analysis and preventative maintenance plan;
- Support the operator in taking corrective actions to either adjust loading rate, loading point or conveyor speed
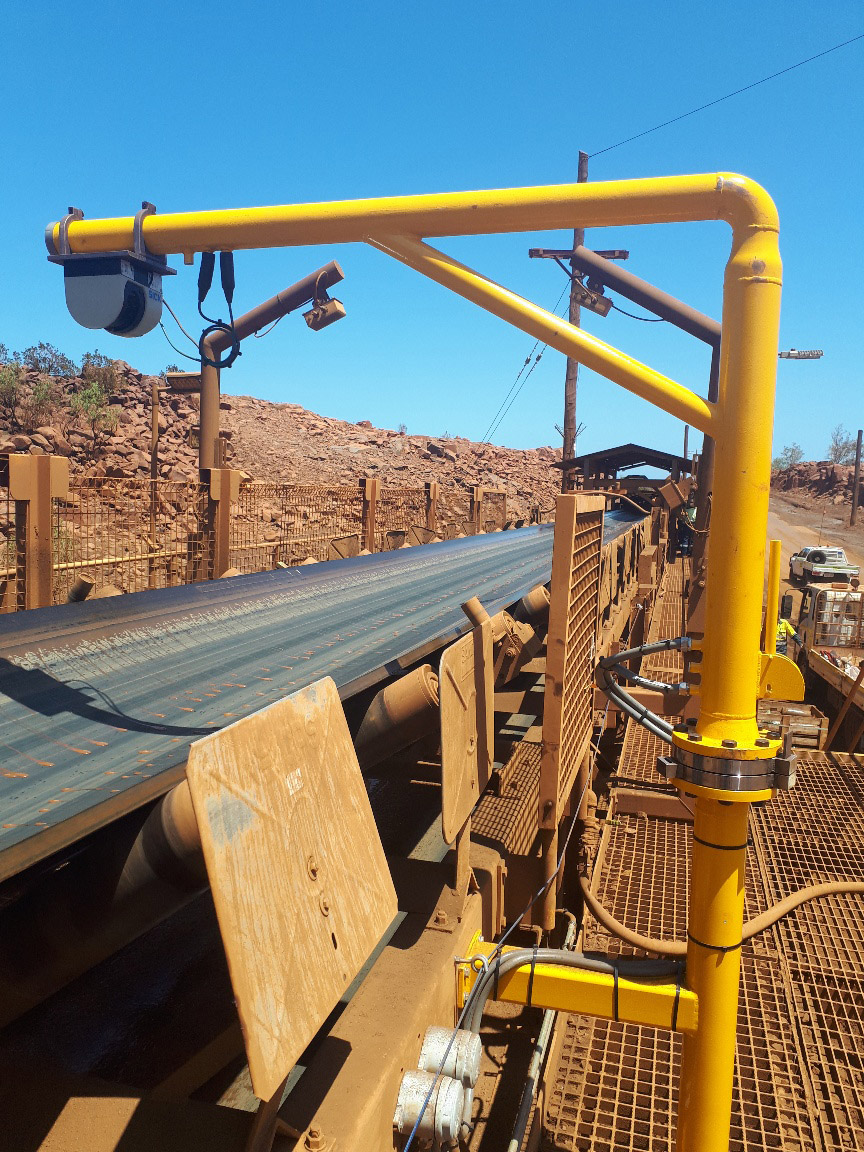
Collision Avoidance System
ACS is a self-contained system designed to prevent collisions between stackers, reclaimers and ship loaders when entering areas of proximity or with other structures.
ACS utilises both existing machine instrumentation to calculate machine-to-machine collision distances or through the addition of active sensors, can detect the presence of objects or structure that may pose a collision risk.
BEC Engineering’s ACS features include:
- Real-time calculation of collision zones across multiple machines
- Data and event logging to Microsoft™ SQL, or a networked database server
- Direct connect to a PLC-based control system for position, status and alarming data
- Independent processing units for maximum flexibility and reliability
- Industrial-grade components to operate in extreme and harsh environments
- Integrated 3D HMI with full diagnostics and condition reporting
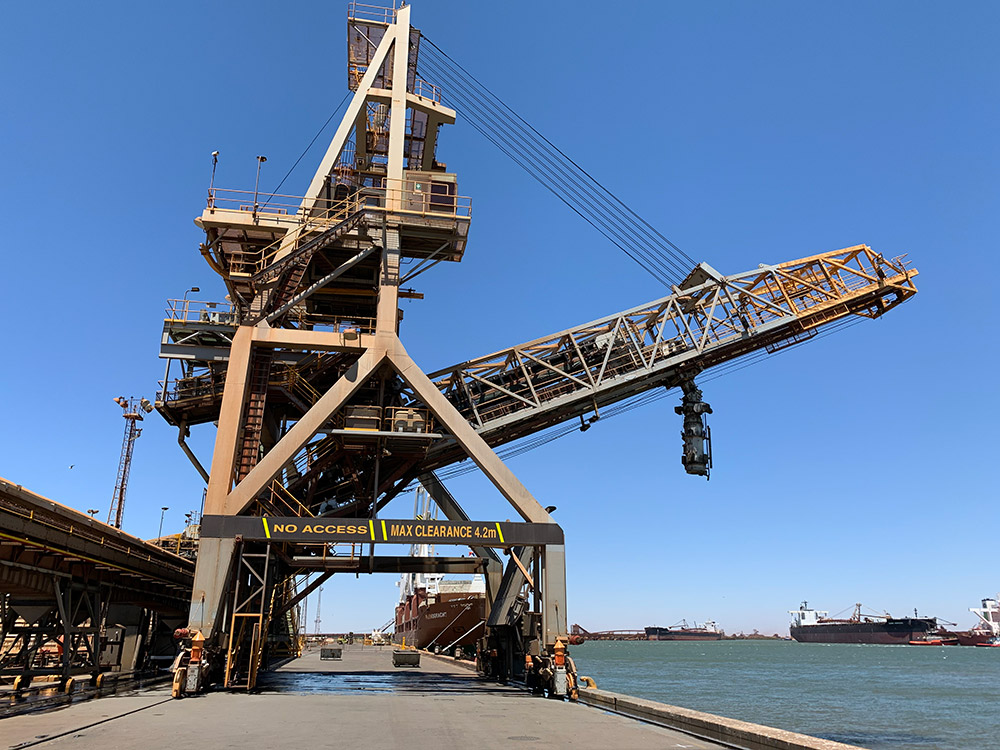
Reclaimer Stockpile Measurement System
The BEC Reclaimer Stockpile Measurement System utlises the latest 360 dgree scaninning radar to measure key stcokpile parameters in order to optimise reclaimer operations. Operating in all weather and environmental conditions, the system provides key metrics to the control system including
- Stockpile Height
- Angle of Repose
- Distance to Face
- Stockpile Edge Positions.
Using this data, the machine control system can be optimised to reduce over torque events from face collapse, elliminate air swings and improve reclaim rates by detecting the edge of the stockpile.
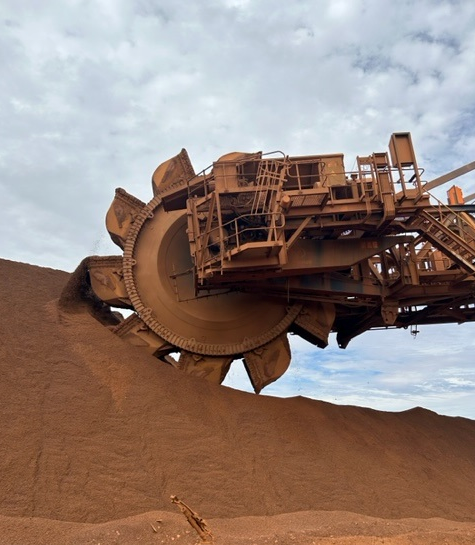
Vessel Berth Monitoring System
Once a vessel is moored in its berth, it must remain as close as possible to its original berthing position to ensure the safe and efficient loading of bulk material into the hold.
Any position change can:
- Effect the ability of the ship loader to follow the loading plan due to the inability of the boom to reach the required hatch loading position.
- Introduce loading delays associated with mooring line tensioning or vessel repositioning.
- Result in uneven mooring line loads or slack that can trigger a line break.
- Result in the vessel leaving its berth pocket, potentially damaging the vessel hull, or running aground.
However, the moored vessel is constantly subjected to wind, wave, and tidal action (current) that, together with the loading of bulk material into its hold, cause the vessel to move.
- Lateral drift – the vessel bow, stern or both moves inward or away from the dock.
- Long drift – the vessel bow and stern move along the dock away from the original bridge wing mark.
The berth monitoring system uses advanced Lidar sensors to accurately measure the relative position change of the vessel in both directions. This information is then communicated to the control system for alarming and reporting.
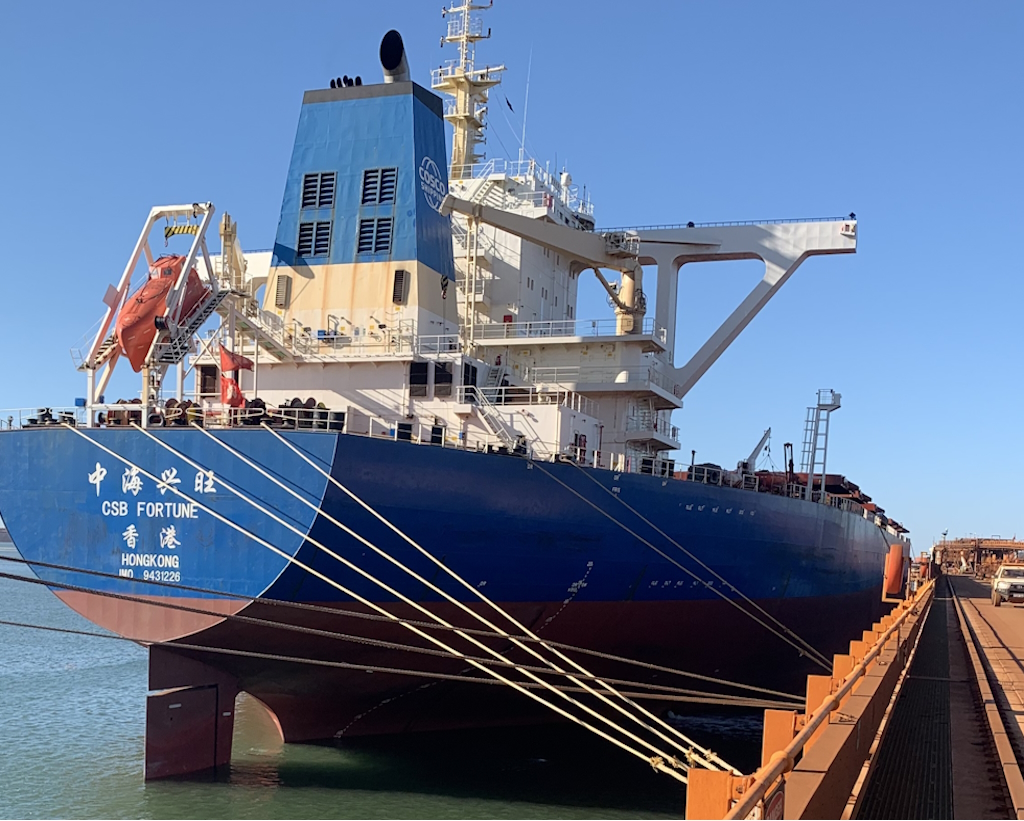
Advanced Volumetric Loading System
The Advanced Volumetric Loading System (AVLS) uses industry leading Lidar scanners mounted above the loading chute to provide:
- High accuracy position tracking of the wagon to ensure precise load control.
- Realtime volumetric profile of the wagon to accurately measure total loaded volume and distribution.
- Combined with the wagon RFID tag, all data can be logged to a central database for reporting and analysis.
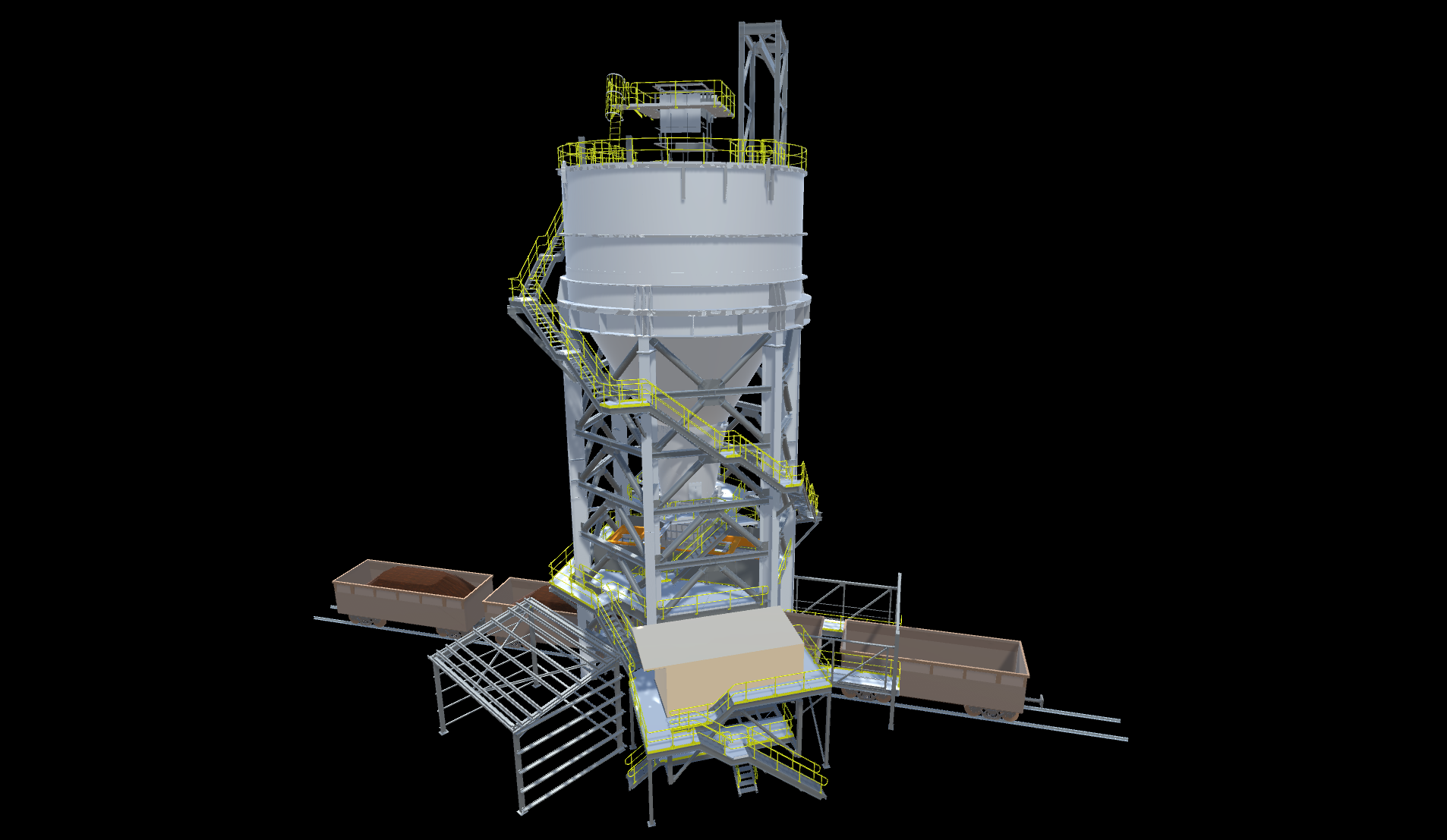